Teste De Solda Mig Mag: Garanta Qualidade Estrutural
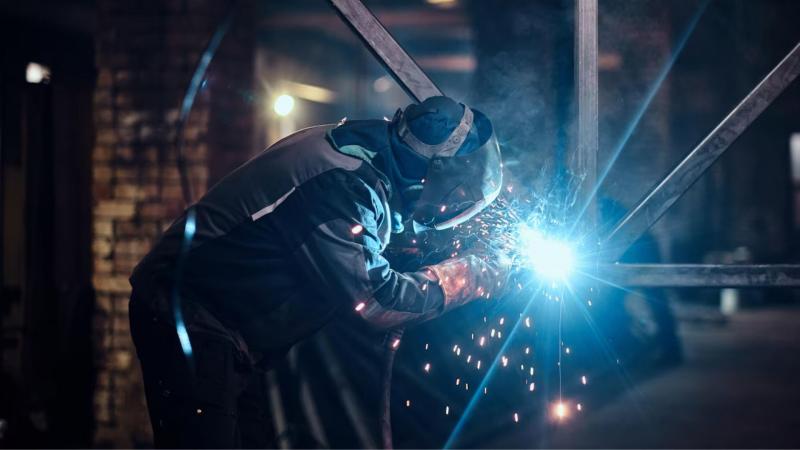
Por: João - 01 de Julho de 2025
A soldagem MIG MAG é amplamente utilizada na indústria devido à sua versatilidade e eficiência. Realizar um teste de solda MIG MAG garante a integridade e a qualidade das conexões, evitando falhas estruturais. Neste guia, você encontrará as melhores práticas e dicas para conduzir esse teste de forma eficaz.
Importância do Teste de Solda MIG MAG
A realização do teste de solda MIG MAG é crucial para garantir a segurança e a durabilidade das estruturas soldadas. Este tipo de soldagem é amplamente utilizado em indústrias automobilísticas, de construção e fabricação, onde a qualidade da solda pode impactar diretamente a resistência e a integridade estrutural dos materiais utilizados.
O teste assegura que os processos de soldagem atendam aos padrões exigidos, garantindo que a junção dos materiais seja eficaz. As soldas bem feitas possuem características adequadas, como penetração correta e a formação de cordões uniformes, essenciais para a performance em condições de uso real.
Além disso, a realização de testes previne riscos e falhas que podem resultar em acidentes, aumentando a segurança no ambiente de trabalho. Um soldador competente que realiza testes regulares em seus trabalhos assegura não apenas a qualidade do produto final, mas também cria uma reputação de confiabilidade com clientes e empregadores.
Os testes de solda também ajudam a identificar pontos de melhoria no processo de soldagem, permitindo ajustes e treinamentos constantes para a equipe. Com isso, é possível reduzir custos de retrabalho e desperdícios, elevando a eficiência operacional e a produtividade do setor.
Por fim, a importância do teste de solda MIG MAG se estende ao cumprimento de legislações e normas técnicas aplicáveis. Garantir que cada solda realizada segue os requisitos normativos é fundamental para a operação e manutenção de sistemas seguros e eficientes.
Equipamentos Necessários para o Teste
Para realizar um teste de solda MIG MAG eficaz, é fundamental contar com os equipamentos adequados. Abaixo, listamos os principais instrumentos e ferramentas necessários para garantir que o teste seja realizado de forma precisa.
1. Máquina de Solda MIG MAG: O equipamento principal para realizar a soldagem e subprocessos de teste. É necessário garantir que a máquina esteja em boas condições de funcionamento e adequada para o material a ser soldado.
2. Equipamento de Proteção Individual (EPI): O uso de EPIs como máscara de soldador, luvas, aventais e óculos de proteção é essencial para garantir a segurança do soldador durante o teste. Esses itens ajudam a prevenir queimaduras e lesões causadas por respingos de metal e radiações.
3. Calibrador de Propriedades Mecânicas: Equipamento que permite avaliar características como resistência à tração e dureza da solda. Esses parâmetros são críticos para determinar a qualidade da união soldada.
4. Ultrassom e Radiografia: Métodos não destrutivos que ajudam a detectar falhas internas ou porosidades na solda sem danificar o material. Esses equipamentos são usados para avaliações mais detalhadas e precisam ser operados por profissionais qualificados.
5. Sensores de Temperatura: Usados para monitorar e garantir que a temperatura da solda atinja os níveis ideais, evitando problemas de fragilidade e outros defeitos.
6. Ferramentas de Medição: Incluindoímetros de folga, paquímetros e goniômetros, que ajudam a verificar as dimensões da solda, alinhamento e outros parâmetros dimensionais importantes durante o processo de teste.
A utilização desses equipamentos não apenas facilita a identificação de falhas potenciais, mas também assegura que o processo de soldagem esteja de acordo com as normas de segurança e qualidade exigidas pela indústria.
Métodos de Avaliação da Solda
A avaliação da solda MIG MAG pode ser realizada através de diferentes métodos, cada um oferecendo insights sobre a qualidade e a integridade da junção. Abaixo, apresentamos os principais métodos utilizados para examinar a solda.
1. Inspeção Visual: Este é o método mais simples e comum. Ele envolve uma análise direta da solda, onde o inspetor busca por defeitos visíveis, como trincas, buracos, falta de material ou cordões irregulares. A inspeção visual é crucial como passo inicial antes de métodos mais avançados.
2. Testes de Resistência: Esses testes avaliam a força da solda sob condições específicas. Testes de tração e cisalhamento são os mais frequentes e ajudam a determinar se a solda é forte o suficiente para suportar as cargas nas quais estará submetida.
3. Testes Não Destrutivos (END): Métodos como ultrassom, raios X e líquidas penetrantes permitem a detecção de falhas internas e externas sem causar danos ao material. Esses métodos são essenciais quando a integridade da peça soldada não deve ser comprometida. Cada um dos testes possui suas particularidades e é escolhido de acordo com as especificações do projeto.
4. Medidas de Dureza: Medir a dureza da solda oferece insights sobre a resistência e a durabilidade. Testes de dureza Rockwell ou Brinell, por exemplo, podem ser aplicados para garantir que a solda possua as propriedades mecânicas desejadas.
5. Testes de Impacto: Neste método, são aplicados impactos controlados à solda para avaliar sua resistência a choques e tensões. Testes de Charpy são comumente utilizados para essa avaliação e ajudam a determinar se a solda irá manter-se sob condições adversas.
6. Teste de Penetração por Líquido: Utiliza um líquido penetrante que revela falhas na superfície da solda. Após a aplicação, observa-se a migração do líquido para identificar qualquer descontinuidade. Este é um método eficaz para detectar pequenas fissuras que não seriam visíveis à simples inspeção visual.
A escolha do método de avaliação deve considerar o tipo de material soldado, as condições de operação e as especificações do projeto. A combinação de diferentes métodos pode proporcionar uma análise mais abrangente da qualidade da solda, garantindo a segurança e a confiabilidade do produto final.
Principais Defeitos a Observar
Durante o teste de solda MIG MAG, é essencial estar atento a diversos defeitos que podem comprometer a qualidade da soldagem. A identificação precoce desses problemas é fundamental para garantir a segurança e a eficácia das estruturas soldadas. Abaixo estão os principais defeitos a observar.
1. Trincas: Resultantes de tensões internas ou externas, as trincas podem aparecer na solda ou nas bordas dos materiais. Elas indicam uma soldagem inadequada ou uma interação negativa entre os materiais. As trincas podem comprometer severamente a integridade da estrutura.
2. Porosidade: Caracterizada pela presença de pequenas bolhas de ar ou gás na solda, a porosidade pode enfraquecer a solda e torná-la mais suscetível a falhas. Este defeito geralmente resulta de contaminação ou de parâmetros de soldagem inadequados.
3. Falta de Penetração: Quando a solda não penetra adequadamente nos materiais a serem unidos, pode resultar em uma junção fraca. Esse problema é frequentemente causado por uma velocidade de soldagem excessiva ou por uma temperatura inadequada da máquina.
4. Excesso de Material: A aplicação excessiva de material de solda pode levar a um cordão irregular e a um desequilíbrio na estrutura da peça. Esse defeito pode causar problemas estéticos e interferir nas propriedades mecânicas da solda.
5. Desgaste das Bordas: As bordas dos materiais podem estar desgastadas ou danificadas, afetando a qualidade da solda. Esse desgaste pode ser resultado de um tratamento inadequado do material antes da soldagem ou de um posicionamento incorreto durante o processo.
6. Unidades de Solda Irregulares: O formato e a consistência do cordão de solda devem ser uniformes. Unidades irregulares podem ser um sinal de problemas no processo de soldagem, como ajustes incorretos na máquina ou na técnica utilizada pelo soldador.
7. Contaminação: A presença de contaminantes, como óleo, graxa ou sujeira, na superfície dos materiais pode resultar em defeitos de solda. A limpeza adequada das superfícies antes da soldagem é essencial para evitar esse tipo de problema.
A observação atenta desses defeitos durante o teste de solda MIG MAG permite ações corretivas imediatas, garantindo a qualidade e a segurança do produto final. A implementação de boas práticas de soldagem e testes regulares pode ajudar a minimizar a ocorrência desses defeitos.
Normas e Padrões para Testes de Solda
As normas e padrões para testes de solda são fundamentais para garantir a qualidade e a segurança dos processos de soldagem. Essas diretrizes estabelecem requisitos mínimos que devem ser seguidos para assegurar a integridade das juntas soldadas, visando prevenir falhas e garantir a durabilidade das estruturas. Abaixo, discutimos as principais normas aplicáveis ao teste de solda MIG MAG.
1. ISO 3834: Esta norma internacional estabelece os requisitos de qualidade para a soldagem. Inclui critérios para o controle de processos de soldagem, documentação e inspeção. A ISO 3834 é especialmente importante para fabricantes que desejam garantir a qualidade de suas soldas e satisfazer as expectativas dos clientes.
2. AWS D1.1: A American Welding Society (AWS) estabelece esta norma para estruturas de aço. Ela fornece diretrizes sobre os métodos de soldagem, os requisitos de qualificação do soldador e as práticas de inspeção. A AWS D1.1 é amplamente utilizada na indústria de construção e engenharia.
3. EN ISO 14732: Esta norma se aplica à qualificação de soldadores e operadores de máquinas de soldagem. Define os requisitos para a formação e certificação de profissionais que realizam solda, garantindo que tenham as competências necessárias para realizar o trabalho com segurança e qualidade.
4. ASME IX: A norma da American Society of Mechanical Engineers (ASME) especifica os requisitos de qualificação de procedimentos de soldagem e soldadores em estruturas metálicas. É amplamente considerada em indústrias de petróleo e gás, onde a segurança é uma prioridade máxima.
5. API 1104: A norma do American Petroleum Institute é aplicável à soldagem de oleodutos e gasodutos. Define os requisitos de soldagem, qualificação de soldadores e inspeção, assegurando que os materiais e processos utilizados atendam aos altos padrões exigidos na indústria.
6. Normas Regionais: Além das normas internacionais, existem normas específicas de cada país ou região que podem ser aplicáveis. É essencial estar ciente das regulamentações locais e garantir que todos os testes de solda estejam de acordo com esses padrões.
Seguir essas normas e padrões assegura não apenas a qualidade das soldas, mas também a conformidade legal e a aceitação do produto no mercado. A integração dessas diretrizes nas práticas de soldagem é vital para a construção de estruturas seguras e de alta performance.
Dicas para Melhorar a Qualidade da Solda
Melhorar a qualidade da solda MIG MAG é uma prioridade para garantir a segurança e a eficácia das estruturas soldadas. Aqui estão algumas dicas práticas que podem ajudar a otimizar o processo de soldagem e obter resultados superiores.
1. Escolha o Material Adequado: Certifique-se de que os materiais a serem soldados sejam compatíveis entre si e adequados para o tipo de soldagem. A seleção correta dos metais e dos eletrodos é fundamental para garantir uma solda forte e durável.
2. Prepare as Superfícies: Antes de iniciar a soldagem, limpe as superfícies que serão unidas. Remova qualquer sujeira, óleo ou oxidação. Essa preparação minimiza a contaminação, o que pode levar a defeitos como porosidade e falta de penetração.
3. Ajuste os Parâmetros da Máquina: Configure corretamente a máquina de solda para a espessura do material e o tipo de eletrodo. Testes práticos podem ser úteis para encontrar a configuração ideal em termos de amperagem, tensão e velocidade de avançar o fio.
4. Mantenha a Distância Adequada: A distância entre o bico de solda e a peça varia dependendo do tipo de solda. Manter uma distância adequada minimiza o risco de falhas e ajuda a alcançar uma penetração adequada da solda.
5. Use um Movimento Consistente: O movimento do bico durante a soldagem deve ser consistente e controlado. Movimentos irregulares podem resultar em cordões de solda irregulares e outros defeitos. Pratique a técnica para desenvolver uma mão firme.
6. Realize Testes de Solda: Antes de soldar em uma grande peça, realize testes em amostras ou sucatas do mesmo material. Isso permite que você ajuste sua técnica e configurações, assegurando que os resultados finais atendam às expectativas.
7. Inspecione e Corrija: Após a soldagem, realize uma inspeção visual para detectar qualquer problema imediatamente. Inspecione as soldas quanto a trincas, porosidade e irregularidades. Um reparo imediato pode evitar problemas maiores no futuro.
8. Mantenha a Manutenção da Equipagem: Realize manutenções regulares em máquinas e equipamentos de solda. Verifique os eletrodos, as mangueiras e as conexões elétricas para garantir que estão em boas condições de uso. Equipamentos bem mantidos produzem soldas de qualidade superior.
Seguir essas dicas pode não apenas melhorar a qualidade da solda, mas também aumentar a eficiência e a produtividade durante o processo de soldagem. Um soldador atento aos detalhes e comprometido com a qualidade conseguirá construir juntas soldadas mais seguras e duráveis.
A realização de testes de solda MIG MAG é essencial para garantir a qualidade e a segurança das estruturas soldadas.
Através da compreensão dos métodos de avaliação, identificação de defeitos e adesão às normas e padrões estabelecidos, é possível assegurar a eficácia do processo de soldagem.
Além disso, a implementação de dicas para melhorar a qualidade da solda contribui para a construção de juntas mais seguras e duráveis.
Investir na formação e na capacitação de soldadores é fundamental para promover práticas de soldagem eficientes, evitando retrabalhos e aumentando a confiabilidade dos produtos finais.
Com o conhecimento e as ferramentas corretas, é possível elevar os padrões de qualidade na soldagem, beneficiando a indústria como um todo.